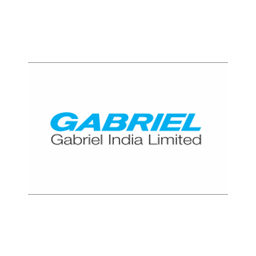
Gabriel India started its operations in 1961, from its factory in Mulund, Mumbai, the company had participated in the development of automotive industry in India and increased its production capacities through presently six facilities and establishing its brand name in OE as well as Aftermarket.
The company has the widest range of Ride Control Products in India and enjoys a leadership position in the market. It has strong presence as a producer and supplier of high quality Ride Control Products for the Indian Automotive Industry participating in all segments i.e. Passenger Cars, Utility Vehicles, Commercial Vehicles and Two Wheelers.
It presently has six plants with a total manufacturing capacity of over 10 million shock absorbers, struts and front forks. The company caters to the requirements of all segments - Original Equipment, Replacement Market and Exports for application in two, three and four wheelers as well as for the Indian Railways.
- Chakan (Pune) - Set up in 1997, this facility delivers suspension products for passenger cars to the widest range of OEMs like Tata Motors, Hyundai, Renault, General Motors, Ford, Toyota Kirloskar & Maruti. This facility is supported by technologies mainly from KYB Corp. that offers suitable products to the foreign auto makers in India. In addition, the company has its fully equipped Product Validation Centre at Chakan which enables it to become self sufficient in designing & developing indigenous solutions suited to its customers.The Chakan plant has several quality certifications like QS 9000, ISO 14001, OHSAS 18001 and TS 16949 apart from many prestigious awards for Innovation and Customer Satisfaction. It also has the mandate to supply suspension products to Renault and Volkswagen.
- Khandsa (Gurgaon) - This is brand new greenfield facility in a most strategic location of Indian Auto giants at Khandsa, with a comprehensive & Integrated Production System [IPS] for manufacture of gas charged shock absorbers. In order to ensure it's leadership, GIL has focussed on implementing several high tech manufacturing processes targeted to meet stringent EU standards. The new technologies are focussed on improving product lifetime under severe weather conditions particularly faced in Europe. The processes that need to be mentioned are Hard Chrome Plating for piston rods - a plant especially designed and built in Germany which has no parallel in terms of quality, product performance and environmental care. It would be the first of its kind facility in Asia Pacific Region including Japan. Further, an in-house Electro-deposition painting system will ensure that product resistance to corrosion will go up several times compared to conventional system. There are many such introductions of 'Leap Technologies' in this plant which takes to a different platform.The plant has commenced production from April 2008 and is meeting domestic requirements of Maruti Suzuki. This facility is slated to deliver suspension products to the European Platforms of Suzuki's new models which are planned to hit the European roads by Dec 2008. The plant will employ 250 people by middle of 2009 and will set a new benchmark in the Indian Auto Industry in terms of its technology and product offerings.
- Dewas- Set up in 1992, Dewas plant has an operating capacity of 4 million nos., employing 320 people and supporting requirements of all commercial vehicles in India like Tata Motors, Ashok Leyland, Eicher, M&M, Force Motors. With its focus on product robustness and precision in delivery, it is able to maintain a dominant position in the commercial vehicle segment.Dewas facility is certified for QS9000, ISO14001, OSHAS18001, TS16949. It is currently working towards the implementation of TPS system and is expected to fully implement it by the year end. The focus area in the future years would be significant increase in productivity.
- Chakan (Pune) for commercial vehicales- Anticipating the growth and demand in commercial vehicle segment, the company has set up an additional facility at Chakan, Pune to produce shock absorbers for commercial vehicles in particular for Bajaj and Tata Motors. Plant also has a modern facility to manufacture new generation products for Indian Railways and heavy duty struts.
- Ambad (Nashik)- Set up in 1991, this facility manufactures Shock Absorbers and Front Forks for two-wheelers (Scooters & Motor Cycles). The technology is provided by 'Yamaha Motor Hydraulic systems, a 100% subsidiary of Yamaha Motor Company, Japan. It has a manufacturing capacity of over 3 Million units and caters to Bajaj Auto, Yamaha & PVPL. The plant is quality certified for TS16949 and is currently engaged in key TPM initiatives.
- Hosur- Set up in year 1997 the company currently has facilities to manufacture 4 million units and mainly caters to TVSM, Suzuki Motors and Yamaha. This plant has made substantial investments to develop innovative products for 2 wheeler market with the backing of Yamaha and KYB of Japan. The plant also exports its products to Japan and supports TVSM, Indonesia for its Indonesian operations.
- Parwanoo- Set up in year 2007, this plant has probably the widest range of product families producing Shock absorbers for commercial vehicle and 2 wheelers, Struts for passenger cars and Front forks for motor cycles. This facility has been created primarily to meet the requirements of replacement market and also optimise the benefits available under special schemes of Govt. of India for hilly regions including Himachal Pradesh. The Company also provides tax optimised products to OEMs who have set-up facilities in tax exempted areas like Uttaranchal and Himachal Pradesh. The facility is expected to optimise its production levels to contribute significantly to the overall business activity of Gabriel India.
- Casting Plant (Chakan)- The company has also taken a major initiative to set up an Aluminium Casting facility at the Chakan campus. This facility will be used to produce Outer Tubes required for making Front forks. Backed by KYB, Japan, it will be capable of making thin walled high strength tubes in India with a special alloy and production process. The facility will be operational by Dec 2009 and products would be used for new generation motor bikes from Yamaha.
The company has overseas markets at Europe, Africa, Middle East, Asia Pacific, China, Russia and Far East.
Gabriel India has financial cum technical collaboration for Ride Control Products with ArvinMeritor Inc., USA, a premier global supplier of a broad range of integrated systems, modules and components to the motor vehicle industry.
In addition, it has tie ups with KYB Corporation, Japan, KYBSE, Spain and SOQI Hydraulic Systems, Japan for product development. The overseas partners extend continuous supporting developing new products to cater to Indian Auto Industry. This includes exchange of technical know-how, special training, regular visits from either side for new projects and continuous improvement.
Awards
• Bajaj Auto Ltd awarded Gabriel India with Quality Gold Award, September 2012
• Gabriel Hosur awarded by TVS Motor Company for completion of the Qaulity Improvement Project 2011 - 2012
• Suzuki Motorcycle India awarded Gabriel India Limited with Quality Performance Award 2011
• Gabriel Nashik presented with 'Best Supplier Award 2011' for Excellence in Supply from Piaggio Vehicles India
• Gabriel Hosur awarded by Honda Motorcycle and Scooter Inda Pvt. Ltd for achieving Quality and Delivery targets, 2010 - 2011
• Gabriel India won the prestigious 'Golden Peacock Eco-Innovation Award' for the year 2012 for its Hollow Tube McPherson Strut specially designed & developed for the first time in India.
• Gabriel India won the first prize in the medium size category of FICCI Quality Systems Excellence Awards for 2012 for manufacturing, a second time in a row.
• Gabriel India won the prestigious Yamaha Special Category Award for 'Contribution to Cost Reduction & VA/VE Activity' for the year 2012, Hosur.
• Gabriel India was selected in the 'India's Best Companies To Work For 2012' study conducted by the Economics Times and The Great Place to Work Institute, India. Gabriel India was ranked third in the Automotive Components section of the study.
• Suzuki Motors India adjudged Gabriel as their Best Quality Vendor for 2012. The award was presented in recognition of Company's exemplary efforts towards quality.